If you are looking to purchase a new table or saw and want a first project or are looking for a significant upgrade to your existing table or saw, take a look at how Mark Chryst with Gunflint Designs created this crosscut sled to gain efficiency, accuracy, and increase safety all at the same time.
Getting Started on Your Crosscut Sled
There are only two hyper-critical parts of a crosscut sled – the runners and the back fence. Other than that, the rest is all just personal preferences and some bells and whistles.
It is critical to have very stable runners that fit without any slop inside the miter tracks in the saw. Many varied materials will work for this, and there are even more opinions on which is best.
Some people will tell you that a good hardwood cut so the grain runs a specific way is the best option. Others will insist on using plywood or MDF because they are less prone to expansion and contraction. I have heard plenty of people find success by buying a cheap plastic cutting board and cutting strips. Some companies sell adjustable runners that you can dial in to fit your miter slots perfectly. There are lots of options, and I have no idea which one, if any, is the best.
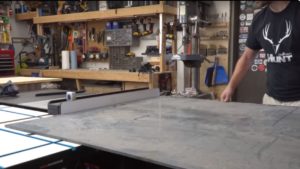
Last year, when I helped clean out my grandparents’ old house, I came across a few four-foot square sheets of what I believe is PVC plastic in varying thicknesses. I saved them and added them to my collection of materials, knowing that, eventually, a project would come up where I needed them. Next, I decided to use this material as the runners for my sled, thinking that they would be impervious to any expansion or contraction, would reset wear longer than any piece of wood, and would have a more slippery surface to aid in sliding down the miter tracks.
I ripped a strip off the edge of my plastic sheet that would be wide enough for two runners and cut the strip in half. I used a caliper to precisely measure the miter slots, which was three-quarters of an inch on the dot, and then I set my fence to a hair over that.
- I wanted them to be oversized to sneak up on a perfect fit.
Moreover, I then cut a strip at that width and then tested the fit in the miter slot. As expected, this first one was too big. I nudged the fence over just slightly, ripped the strip, and tested it again. I could get it to fit this time, but it was tight and did not slide well. This is precisely what I was looking for, so I ripped the second strip to the same size. I cut four runners while everything was set up, knowing that I had more sleds coming up, and I did not want to dial this in again next time.
I hand-sanded the edges of the runners with 220-grit paper until I had the EXACT fit I was looking for. They slid back and forth effortlessly but had no discernable play side to side.
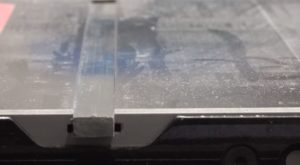
With my runners ready to go, I focused on the fences. Once again, materials have many possibilities here, but the focus should be on something that will not move and warp once you have the fence set square. Some people do this by laminating several pieces of plywood to get one thick piece. I had a massive beam of rough-cut cedar drying for ten years. Moreover, it has the added benefit of being lightweight wood, so my sled would not be too heavy once it was finished.
I used a jointer and planer to get the two fence pieces perfectly flat, square, and down to the thickness I wanted. Then, I used the table saw to rip them to their final height and cut them to length. I tipped the blade on the table saw to 45 degrees and shaved about an eighth of an inch off one corner.
This creates a small recess in the back fence. Without this recess, the dust gets trapped in between the wall and the workpiece and will throw off the cut. With the recess, the dust slides harmlessly out of the way, keeping your cuts more accurate.


For the main body of the sled, I used three-quarter-inch MDF. The overall size I am going for is arbitrary. I wanted it to be big but let the materials I had on hand dictate the specific dimensions.
Start Assembling your Crosscut Sled

The first step in assembly is attaching the runners to the body. I put several washers in the miter slots to lift the runners higher than the table’s surface. Then, I ran a thin bead of CA glue down the entire length of the runners. This must be enough to hold the runners to the body while you flip the whole thing over. Ensure you do not use it so much that there is a squeeze-out. You would not want to glue your unfinished sled to your table saw.
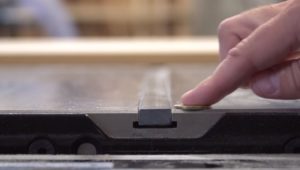
I locked the table saw fence down and then used it as a reference to push the MDF sheet against. This way, I could slowly lower the sheet down onto the runners while keeping everything lined up and as square as possible. With it set in place, I pressed down on the runners to make sure the glue made contact; then, I walked away for a few minutes to let the glue set up. Most of the time, I use an accelerator with CA glue to speed up the process, but in this case, I did not want to use any on the MDF since MDF sucks up moisture like a sponge, and I was afraid this would hurt the flatness of my sled.
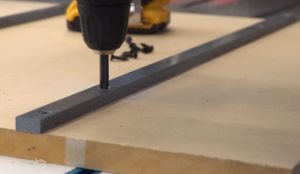
Once the glue dried, I carefully pulled the runners out of the miter slots and flipped the sled upside down. I drilled pilot holes every few inches along the length of both runners using a flag on my drill bit to ensure I did not drill all the way. Then I used a counter sink bit on all the holes to make sure all the screw heads would be recessed below the surface of the plastic. After driving in a bunch of three-quarter-inch screws, the slides are locked down for good.
I flipped the sled back over and put the runners in the miter slots to test how well they slid. They moved, but they were binding up just a bit, so pushing and pulling the sled took too much effort. I flipped it back over, then used a scrap of wood with a square corner wrapped with some 220 sandpaper and slid it back and forth along both sides of each runner. The fit was already so close to perfect that I did not want to remove too much material, so I only made a few passes before flipping it back over and testing the fit. The sled moved back and forth effortlessly this time, but there was ZERO side-to-side movement.
Moving on to the fence, I lined up the right corner and made the back of the wall flush with the sled’s base. This will not be perfect, but it is close and an excellent place to start. I clamped the pieces together, then drilled a pilot hole from the bottom and ran in a screw to hold this corner in place.
I needed to cut a reference line in the MDF by raising the blade through it, so I temporarily removed the receiving knife from the table. Then, with the saw running, I turned the crank until the blade started to poke through the middle of the board. Pushing on the base, not the fence, I slowly slid the whole thing forward until the blade had cut right near the wall.
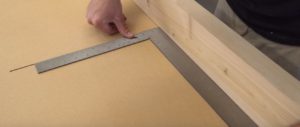
I grabbed my giant square and, referencing off the cut line, pivoted the fence until it was as square as possible. Then I clamped down the left corner, drilled a pilot hole, and ran in a screw.
The front fence does not have to be perfectly square to the blade. So, I just flipped the sled over, lined up the back edges of the wall and the MDF, then screwed it in place, putting a screw in each end, as well as close to both sides of the saw line.
- This way, none of the parts will move around when I cut through the MDF.
The 5 Cut Method Checks for Accuracy
Here is where we start testing and adjusting the rear fence to perfect it. I am using a commonly known process called the 5 Cut Method. You take a scrap of wood and cut off one side, then put the freshly cut side up against the fence and cut the next. You continue to do this until you get around, then cut a one-inch strip off the side you started with.
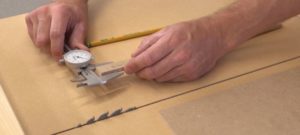
Make sure you mark the front and back of that strip, then measure each end to see how different they are. At this point, some math is involved. If you do everything correctly, you will eventually produce a number that tells you exactly how much you must adjust your fence to get it square. To make my adjustment, I found a feeler gauge that matched the number I produced. I had to move the left side of my fence forward, so I put the gauge up against my fence, then put the point of a carpenter’s pencil against it and clamped it down.
I removed the screw from the underside of the fence and carefully nudged the fence forward until it just barely touched the tip of the pencil. Then, I did the following:
- Clamped the wall in that position.
- Drilled a new hole.
- Ran in a screw.
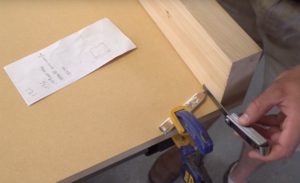
With the new fence position locked in, I performed the test again. I had reduced my previous error by more than half this time, but I still wanted it to be better, so I just repeated the process. It took me three times before I had my fence as precise as I wanted, but you could keep doing it as many times as it takes to make you happy.
Finishing Touches
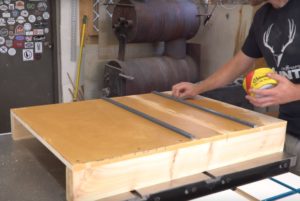
With my fence dialed in, I flipped the sled over and put screws in both the front and back fences every few inches to keep them from moving around. I made sure to have screws close to the cut line but not so close they were in any danger of touching the saw blade. I rubbed paste wax into the bottom of the sled and over the runners to help reduce friction and keep it gliding effortlessly over the saw.
The Final Change
The final change was adding a bit of safety to the sled. I glued a scrap block of cedar to the back of the fence. This way, when the blade passes through the wall, it is contained inside this wood block and does not present a danger to my fingers. I only used CA glue when mounting this block because I have not decided if this is my permanent solution to this problem. If I change my mind, I can tap this off with a hammer and do something else.
This is the most excellent and precise crosscut sled I have ever had in my shop, but it is still fundamental compared to some of the sleds out there. I left the top of my fences flat and square just in case I wanted to install a t-track. A t-track would be helpful because it adds some modularity for adding other jigs or a flip stop to the sled. If you knew this was not something you wanted, there are different shapes you could use to make your fence.
A popular one looks like an elongated oxbow where the highest point is just over the blade line to hold everything together; then, it sweeps down so the rest of the fence is at a lower maximum height. This design looks cool and makes getting your hands over the wall and holding down your workpiece much easier.
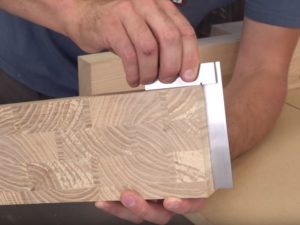
I have made a crosscut sled in its purest form: no frills, just a large capacity, durability, and precision. If you have never made a crosscut sled before, you NEED one, and this is a beautiful place to start.
Mark Chryst of Gunflint Designs created the Video and Blog Post in partnership with Acme Tools. Check out more of Mark’s work on his blog or his Gunflint Designs website.
- Check out the Acme Tools Table Saw Buying Guide to learn more about which table saw to purchase.
- Check out our Acme Tools How to Choose a Table Saw for a great infographic that makes the selection process manageable.
Want to let us know how much you liked this post? Click on the start below or leave us a comment. You can always include us in your social media feed by tagging us with #DoYourBestWork. Acme Tools is active on Facebook, Instagram, Twitter, and Pinterest.